Application of FRP as a Construction Material for Wet Scrubbers, Internals, and Ducts in the Cement Industry
Plasticon Projects specializes in delivering high-quality, corrosion-resistant Fiber Reinforced Plastic (FRP) solutions for the cement industry. The preheater tower, calciner, and rotary kiln play a crucial role in cement production but generate aggressive flue gases, including sulfur oxides (SOₓ), nitrogen oxides (NOₓ), carbon dioxide (CO₂), and acidic compounds. To effectively manage these emissions, cement plants require durable wet scrubbers, internals for wet scrubbers, and ducting systems after the scrubber.
At Plasticon Projects, we design and manufacture FRP-based wet scrubbers, internals, and ductwork, offering long-lasting, low-maintenance, and cost-effective solutions for cement plants.

FRP for Wet Scrubber Systems in Cement Plants
The Role of Wet Scrubbers
Wet scrubbers are essential in removing SOₓ, dust, and acidic gases from exhaust streams before they exit into the atmosphere. These systems operate in highly corrosive and high-moisture environments, making FRP the ideal material for construction.
Why Choose FRP for Wet Scrubbers?
- Corrosion Resistance: FRP withstands acidic environments, preventing structural degradation.
- Lightweight & Durable: Easier to install and maintain compared to traditional steel.
- Cost-Effective: Minimal maintenance requirements lead to lower operational costs.
- Thermal Insulation: Reduces energy loss and improves system efficiency.
- Customizable Design: FRP can be molded into complex shapes for enhanced performance.
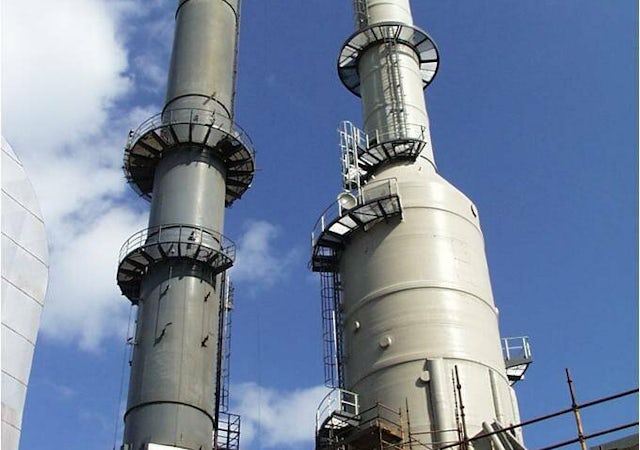
FRP for Internals in Wet Scrubbers
Challenges in Wet Scrubber Internals
The internals of wet scrubbers, including mist eliminators, packing media, and baffles, are exposed to continuous moisture, acidic gases, and high particulate loads. Traditional materials like stainless steel corrode over time, leading to frequent replacements.
Benefits of FRP Internals
- Superior Chemical Resistance: Handles acidic condensates and chemical reactions efficiently.
- Enhanced Wear Resistance: FRP coatings extend service life by reducing material degradation.
- Lightweight Structure: Eases installation and maintenance procedures.
- High Efficiency: Improves gas-liquid interaction for optimal pollutant removal.
By integrating FRP internals, Plasticon Projects ensures long-term performance and minimal downtime for cement plant operations.
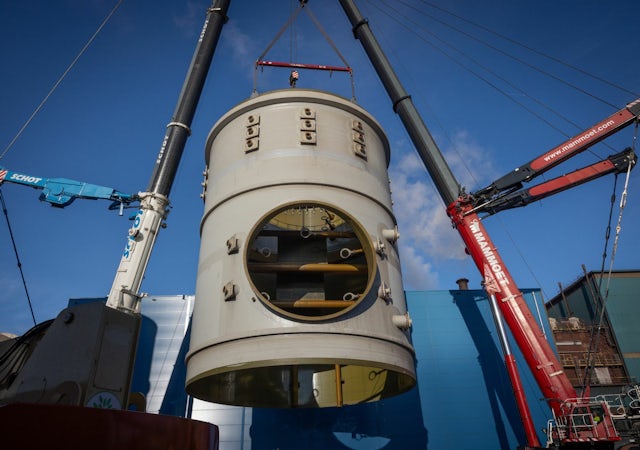
FRP Ducting After the Wet Scrubber
Importance of Ducting in Cement Emissions Control
Ducts transport scrubbed flue gases from the wet scrubber to the next stage of processing or release. These ducts operate in high-moisture and high-temperature conditions and are prone to acid condensation and structural failure if made from conventional materials.
Why FRP is the Best Choice for Ducting Systems?
- Exceptional Corrosion Resistance: Withstands acidic and alkaline condensates.
- Lightweight & High Strength: Reduces stress on supporting structures.
- Minimal Maintenance Needs: Eliminates frequent repairs and replacements.
- Custom Design Flexibility: FRP ducts can be tailored for various plant configurations.
- Extended Service Life: Ensures long-term durability, reducing lifecycle costs.
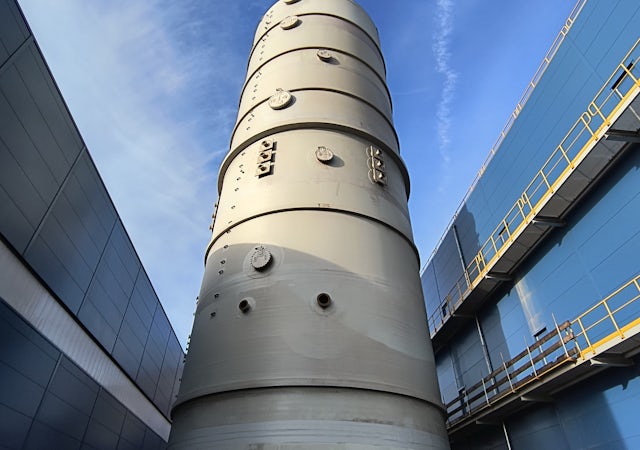
Why Choose Plasticon Projects for FRP Solutions?
At Plasticon Projects, we are pioneers in FRP-based wet scrubbers, internals, and ducting systems. Our solutions are engineered for maximum durability, cost efficiency, and environmental compliance. We help cement plants improve their emission control systems while ensuring seamless integration, high performance, and reduced operational costs.
Key Benefits of Working with Plasticon Projects:
- Expertise in custom FRP fabrication
- Industry-proven high-performance materials
- Turnkey solutions tailored to cement plant requirements
- Sustainable and cost-effective alternatives to traditional materials
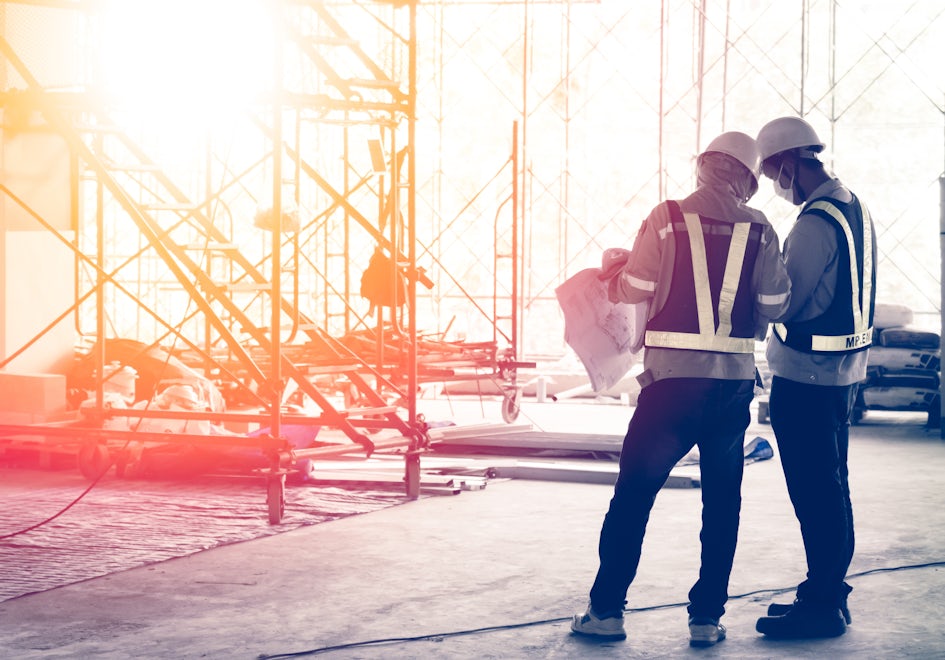