The installation of a corrosion resistant fiberglass chimney liner in a concrete chimney at the Turów (Poland) power plant
Case study: FRP chimneys and ducts, including by-pass system for Power Station Turów
Written by J.W. Warnar
Year of publication: 2016
Plasticon Composites International Contracting BV
Location: Hengelo, Overijssel, The Netherlands
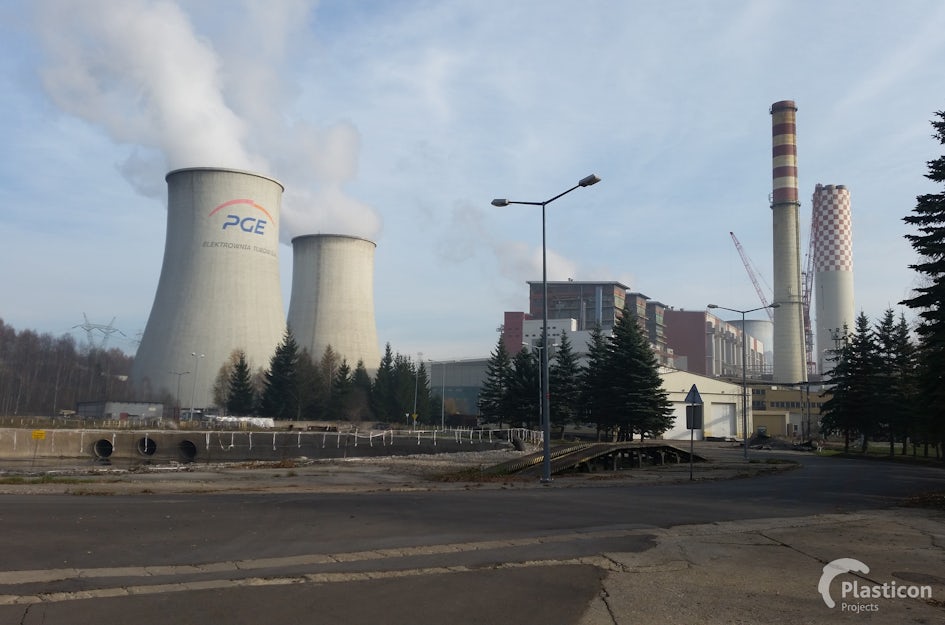
Abstract
PGE Group, Polska Grupa Energetyczna, a major energy group in Poland invested in environmentally friendly equipment and modernization of its existing power stations. Part of this investment was the order of three new ‘Flue Gas Desulfurization’ units, based on spraying of lime-stone suspension into flue gas (wet FGD). The units were designed for the lignite and biomass fuelled units 4, 5 and 6 of the Turów power plant in Bogatynia, Poland.
Each unit is designed for a maximum flue gas flow of 1,280,000 Nm3/h with a maximum SO2 concentration of 2,500 mg/m3 and a removal of ≥ 97.5%. After the installation of the three lines, the flue gas desulphurization unit operates at a temperature of 70°C and normal conditions. However, during the construction period, the flue gas desulphurization of unit 4 and 6 were not operative: during this period the units operated under by-pass conditions. As soon as the last unit (number 5) was installed the total system was operational for flue gas desulfurization.
During by-pass operation (Unit 4, 2 years) the temperature of the system could reach temperatures up to max 160°C (for two hours, normal 141°C) and under a maximum SO2 concentration.
The three existing chimney liners, consisting out of borosilicate blocks, needed to be replaced as this lining material was not the right choice for the flue gas desulphurization unit of this new power plant. The engineers of PGE decided to use fiberglass reinforced plastics, FRP, for the construction of the 700 meter high chimney liners and all duct systems due to the wet circumstances and the huge differences in temperature (20 – 160 °C).
The challenge of this project for Plasticon Composites was the short construction time that was given by PGE Group. PGE insisted in demolishing the brick chimney liner and installing the new fiberglass chimney liner within a time frame of 40 days. At that point Plasticon Composites only had 25 days to install a new chimney liner of 5,300 mm in diameter and 120 meters high.
This paper will describe the realization of this challenging installation job Plasticon Composites executed, as well as the possibilities of fiberglass and the construction method of a fiberglass chimney liner and duct.

Location: Bogatynia, Poland
Flue Gas Desulphurisation at The Turów (Poland) Power Station
Project scope
The Turów power plant consists of six blocks of 200 MW. To meet the environmental requirements the PGE group decided to invest in flue gas desulphurization (FGD) for three of the existing production lines (unit 4-6). The three existing chimney liners needed to be replaced with another material because the existing liners were not resistant to the new FGD conditions, besides, these liners were already in use for more than 10 years.
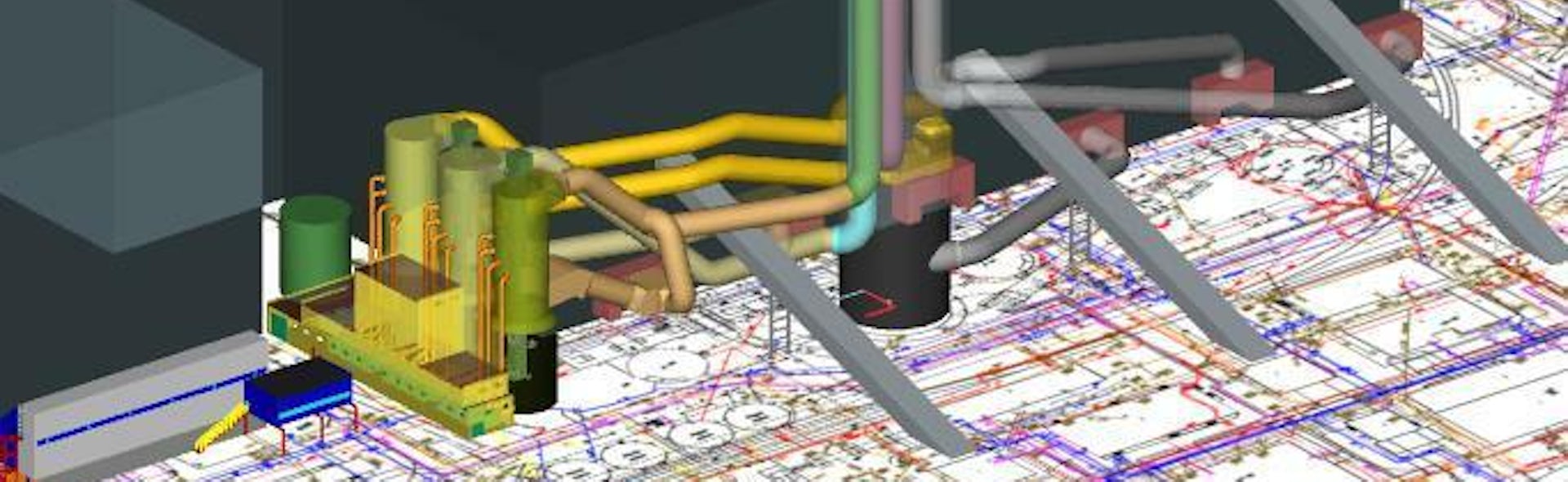
Figure 1: The lay out of the power plant with FGD for unit 4-6.
The FGD system for unit 4 – 6 consists out of a chimney liner of 120 meters each and about 330 meters of duct work. The diameter of the total system was 5,300 mm.
Design criteria
Introduction
In 2010 PGE made a feasibility study for the selection of the right material for the absorbers, the ducts and chimney liner. Based on the following criteria they decided on fiberglass reinforced polyester, FRP, to be the right choice for the flue gas desulphurization unit of this new power plant. The criteria:
- Chemical (and corrosion) resistance
- Temperature resistance
- Ash load
- Lifetime and guarantee period
- Installation time of the chimney liner
- Cost
Chemical resistance
Each unit is designed for a maximum flue gas flow of 1,280,000 Nm3/h with a composition of the gas according to table 1.
Flue gas composition
The engineers of PGE decided the three existing chimney liners, consisting out of borosilicate blocks, needed to be replaced because of two reasons: First, because of the wet circumstances of the FGD system. Secondly, due to the concentration of hydrogen fluoride (HF) in the gas flow. To meet these operating conditions, fiberglass, alloy or titanium cladded steel would be the right construction material.
Temperature resistance
Normally, the flue gas desulphurization unit would work at a temperature of 70°C. However, during the construction period the flue gas desulphurization of unit 4 and 6 would not be operative, these units would have to operate under by-pass conditions, reaching higher temperatures than normal. As soon as the last unit (5) was installed, the total system would be operational for flue gas desulfurization.
During by-pass operation (unit 4 in two years’ time) the temperature of the system can reach temperatures up to max 163°C (for 2 hours, normal 141°C) and under maximum SO2 concentration. The design of the system was based on 22 shut downs per annum. These large repetitive differences in temperature (20 – 160 °C, 22 shut downs per annum) were very important in deciding the right construction material. Fiberglass can perfectly withstand these extreme temperature differences.
Ash load
The expected ash load in the ducts (150 kg/m2), the weight of the duct itself and the insulation properties of the material were important criteria for the design of the steel support construction. FRP is lightweight material, especially compared to steel with borosilicate blocks, meaning a saving of 25-30% on steel supports in design was achieved. On top of that, fiberglass is also better resistant to the excessive quantity of condensate that accumulates in the duct sections, due to excellent insulation properties.
Lifetime and guarantee period
PGE insisted on a long lifetime (> 30 years) of the process equipment and therefore asked for a guarantee period of five years, based on the maximum design data. Fiberglass can easily hold this lifetime, specifically under circumstances during flue gas desulphurization. The first fiberglass liners for FGD already were installed in 1973 in Salt Lake City in the USA (Brady 2015) and 21 years ago in Ingolstadt Germany (van Buren 2014). The first stacks for waste incineration plants, where the design conditions are generally more extreme, were installed in 1985 at the Rotterdam waste incineration plant (AVR).
Based on the experience with FRP, a guarantee period of 60 months or five years after commissioning of the power plant was no issue. This demand could easily be fulfilled by Plasticon Composites.
Installation time of the chimney liner
PGE insisted in demolishing the old borosilicate brick chimney liner and installing the new chimney liner within a time frame of 40 days. Plasticon Composites had 25 days to install a new chimney liner of a diameter of 5,300 mm and 120-meter height plus corresponding by-pass section, while the other five blocks of the power plant remained in operation. This short installation time would avoid a long shutdown of the power plant, meaning high costs.
The power plant was fully occupied so loss of one line during an extended period time was very expensive and impermissible. PGE already planned the investment of an extra block of 200 MW to fulfil the needs of their client. Plasticon Composites presented a very detailed plan for the installation of a new fiberglass chimney liner in maximum 25 days. The installation of the first liner including by-pass took 25 working days. The installation of the last liner was ready within 19 working days.
Cost
PGE also made a cost comparison of different materials and came to the same conclusion as had been presented by Mr. Victor Bochicchio at the ICCT conference in Prague in 2014 (see tab. 2).
Cost of lining materials
Conclusion
Based on the above mentioned design criteria, the engineers of PGE have written a design specification and advise to apply fiberglass material for the construction of the chimney liners, duct systems and by-pass system. FRP material proofs to have good mechanical properties and it has excellent chemical resistance. Furthermore, its temperature resistance properties and the fact that the material has a long life time are important criteria to select the preferred material. And last but not least, the competitive pricing for the construction of an FRP chimney liner and duct work contributes to the statement that the application of FRP is a well thought out solution.
Production of the chimney liner and ducts
Filament winding of the fiberglass reinforced polyester (FRP) cans
First of all, the chimney liner was designed according to the most extreme design conditions by making a static calculation
according to the CICIND, EN or ASTM standard. This static calculation was checked by executing a Finite Element Analysis
(FEA) taking into account the loads caused by pressure, temperature, ash, weights etc.


Figure 2: The FEA of the chimney liner unit 4
Besides this static calculation, a flow analyses and condensate calculation was be prepared.
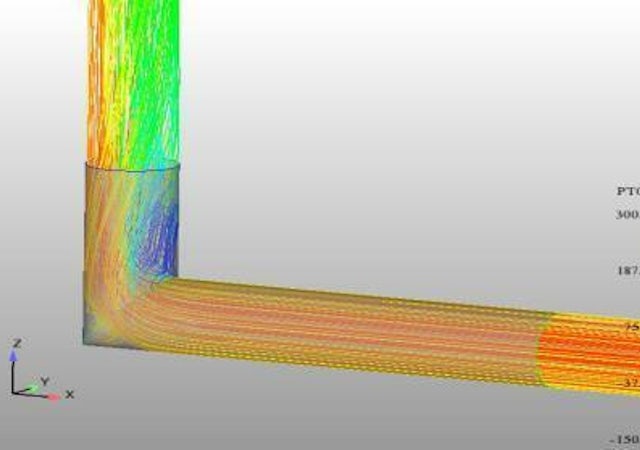
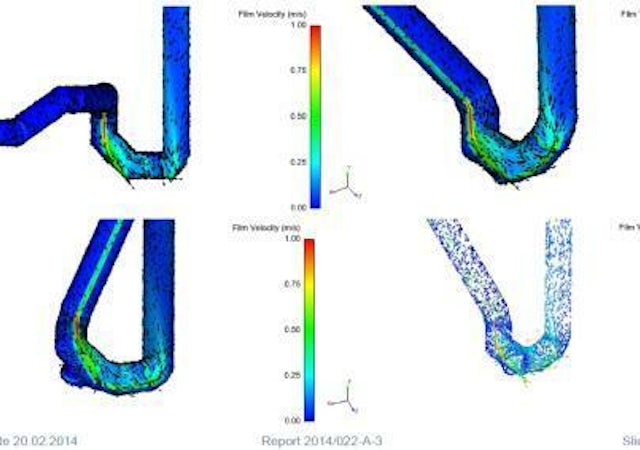
Figure 3: The flow analysis of a duct in a cooling tower and a condensate calculation of unit 4 of the chimney liner of Turów.
Big diameters chimney liners and ducts are produced on site in a temporary facility, named the ‘On Site Winding Machine’ (OSWM). This facility needed to be temperature controlled in summer (temperature up to 45°C) and winter (temperatures as low as -35°C) time. The OSWM is to be built out of ISO containers or a double wall tent. In this temporary facility the cylinder or cans of 6-meter or 10-meter height (depending on the used machine) are built by filament winding. Every can consists out of a chemical barrier layer (2.5 mm) and reinforcement layers based on DERAKANETM 470 HT Epoxy Vinyl Ester Resin (a high temperature resin) and winding- and spray roving. For ducts the reinforcement layers were built with uni-directional core-mats in order to give longitudinal strength because of bending of the ducts between two supports. For the project in Turów, Plasticon Composites produced ± 700-meter pipe or 126 cylinders in about 14 months.
Pre-assembly of the cans
In order to fulfil the condition to install the chimney liner within a time frame of 25 days, Plasticon Composites prepared segments of 24 meters, made out of four cans. These segments were still easy to handle (approximately 25 ton) and could be lifted by the crane.
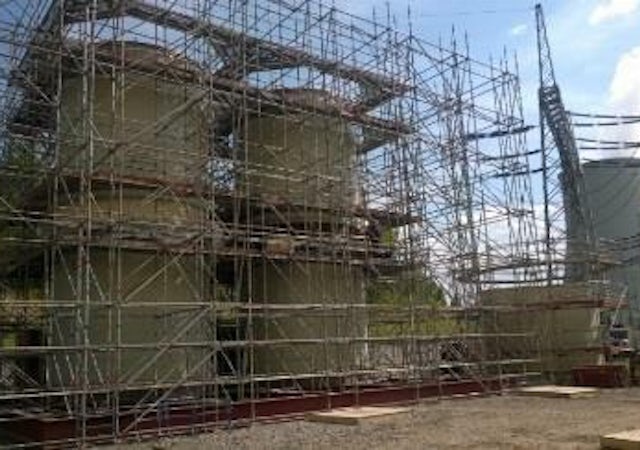
Figure 4: Pre-assembly of the cans.
Installation of the chimney liner and ducts
Demolition of the existing chimney liner
A subcontractor of PGE took care of the demolition of the existing chimney liner. They removed every borosilicate brick via the lower exit of the concrete stack. During this demolition it was not possible to prepare the new chimney liner in the concrete stack although the space was there. It was not safe, and during the demolition a lot of dust was produced. The demolition of the brick liner took 15 days.
Installation of the chimney liner Unit 4
Plasticon Composites made a detailed installation planning to secure the maximum installation period of 25 days would not be exceeded and to avoid a possible penalty of € 85,000 per day due to a longer shutdown of the power plant. It was clear that the installation of the new chimney liner could not be done in the lower part of the concrete stack. The demolition of the brick liner caused a lot of dust and HSE conditions could not be assured. This meant the installation had to be done using the inlet or the outlet of the concrete stack. As the inlet was blocked during demolition and the time frame (25 days) was too short to build the new fiberglass chimney liner and by-pass out of the 25 cans of 6 meters, this was not an option.

Figure 5: Installation of the pre-assembled cans.
So, using the outlet was the only option. By building segments of 24 meters, the installation could be set on 25 days. In this period the cans of 24 meter, the liquid collection system, the rain hood, the elbow, the by-pass, and all steel supports were installed and the total lamination work had been carried out by working in two shifts.
Installation of the duct work
The installation of the ducts were separately executed. All ducts are insulated with a 50 mm PU insulation in order to avoid condensation. Although fiberglass is an insulator in comparison with steel, PGE demanded to insulate all parts outside the concrete stack. The insulation of the fiberglass cans were directly done at the production of the can so it is a closed structure and highly insulated. The ducts have been installed in segments of 23-meter length and 26 tons in order to prevent disturbance during installation of all other components in the power plant, by using the maximum capacity of the huge tower crane.


Figure 6: Transport and installation of the duct work.
Developments in the FRP business
Variable mould
Every chimney liner or duct work in fiberglass has its own dimensions due to the capacity of the power plant and the process design of the flue gas desulphurization. In order to be competitive, Plasticon Composites designed a variable mould in order to produce every diameter with one single mould. This mould is built out of fiberglass lamellae and can be varied from 7 till 12.5-meter diameter or 12 till 20-meter diameter.
FRP Absorber
Now that it was possible to produce big diameter fiberglass chimney liners, ducts and tanks on site, the engineering companies are also interested in producing big diameter absorbers in fiberglass, instead of the conservative materials like concrete/PP or flake lining or steel/rubber. The disadvantage of these materials is their high corrosion, long construction time and cost. The first absorbers were already built in the eighties in the USA and nineties in Europe. A nice example are the two absorbers of 9-meter diameter and 49-meter height at the power plant of PCK Schwedt. It is even possible to produce absorbers up to a diameter of 30 meters.


Figure 7: A fiberglass scrubber of 30-meter diameter.
The absorbers of the Bowen power plant, built in 2007, have a diameter of 30-meters and a height of 20 meters. These absorbers, 4 in total, are designed according to the Chiyoda license.
References
Bochicchio V, 2014. An overview of lining materials for use in the renovation of existing power plant chimneys, ICCI 2014 Prague.
Brady B, 2015. Development of GRP in the chimney industry, CICIND Conference 2015 Boston.
Buren, van A, 2014. Composite solutions as problem solvers in industrial chimneys and cooling towers, ICCT 2014 Prague.
Plasticon Projects is ready to support you in every way
Together we can reach the top
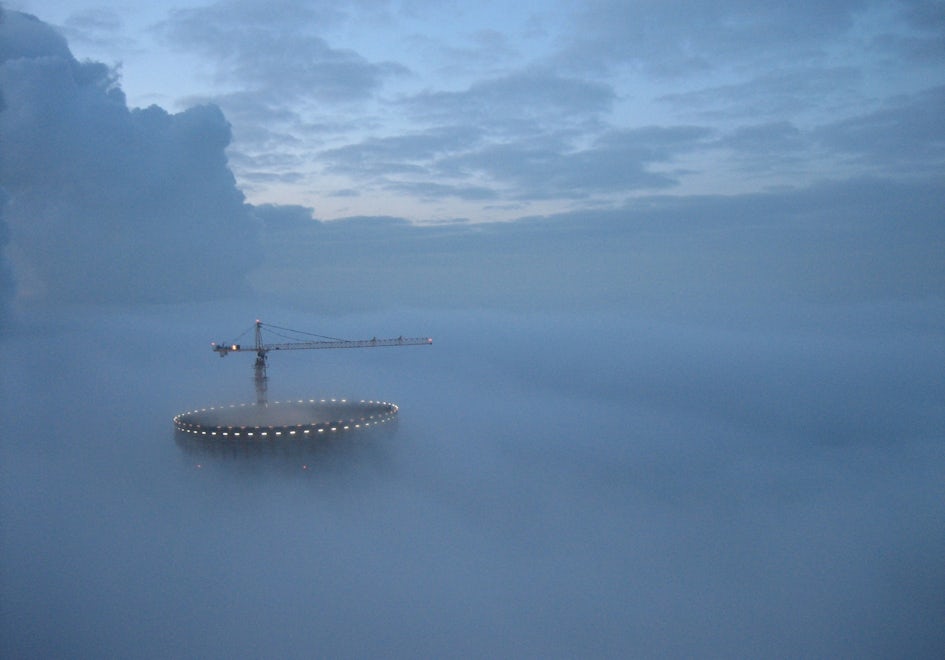