Fiberglass Reinforced Plastics
Fiberglass Reinforced Plastics (FRP) are transformative materials powering diverse industries with their versatility and resilience. Comprising a blend of polymer matrix, typically thermosetting resin, and reinforced fiberglass fibers, FRP composites deliver unparalleled advantages. This article delves into the myriad benefits of FRP and its pivotal roles in tanks, absorbers, piping, and flue gas ducts, showcasing its exceptional utility in critical applications.

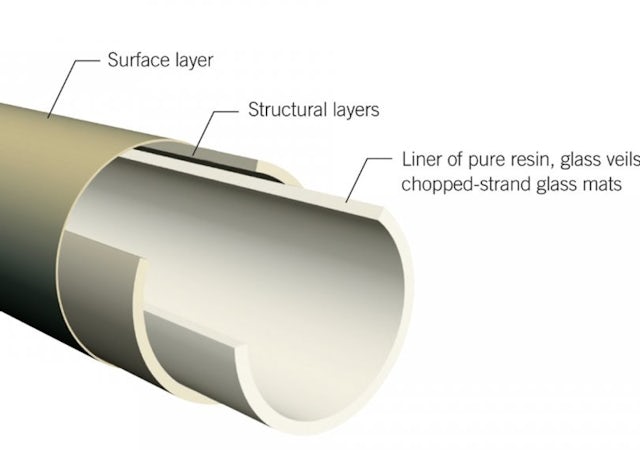
Understanding FRP
FRP, or Fiberglass Reinforced Plastic, is a composite material comprising thermosetting resins and fiberglass. This fusion of resin and glass fibers forms the core of FRP products, delivering robust structural integrity and durability. The resin provides vital environmental and chemical resistance while binding the glass fibers in the structural laminate. Selection of resin type is tailored to specific chemical and environmental conditions as per user requirements. At Plasticon Composites, FRP products typically feature three distinct laminates:1. Corrosion barrier: Ensures chemical and temperature resistance.
2. Structural laminate: Provides essential temperature resistance.
3. Topcoat: Enhances environmental and temperature resilience.
Each laminate serves a unique purpose, necessitating the selection of appropriate resin types. Plasticon Composites primarily employs three resin types - polyester, vinyl ester, or epoxy.
Moreover, glass selection is crucial, determined by application requirements and manufacturing processes, including different types of veils. The meticulous composition of these elements, coupled with precise resin selection, winding techniques, and glass fiber components, ensures the quality and benefits of FRP materials. Choosing the right manufacturer is paramount in guaranteeing product excellence and performance.
Unlocking the Benefits of Fiberglass Reinforced Plastics (FRP)
Corrosion Immunity
FRP stands out for its exceptional resistance to corrosion, a quality unmatched by traditional metal materials. Resilient against acids, bases, and salts, FRP remains steadfast even in the harshest environments. Industries grappling with corrosive challenges, such as chemical processing, wastewater treatment, and marine operations, find solace in FRP's enduring protection.
Strength Amplified by Lightness
FRP composites boast an impressive strength-to-weight ratio, thanks to the amalgamation of fiberglass and resin. Despite its featherweight quality, FRP stands firm against formidable mechanical pressures. This characteristic renders it indispensable for structures necessitating robustness without bulk, exemplified in tanks and piping systems.
Tailored to Perfection
The adaptability of FRP knows no bounds, as it can be sculpted into myriad shapes and sizes to meet specific demands. This inherent flexibility proves invaluable in crafting bespoke components for tanks, absorbers, piping, and flue gas ducts, accommodating their unique contours and specifications.
Shielded from UV Assaults
Resistant to the sun's relentless UV rays, FRP materials thrive in outdoor settings. Unlike conventional plastics prone to degradation under sunlight, FRP retains its structural integrity, making it an optimal choice for components exposed to the elements.
Guarding against Temperature Extremes
FRP offers superior thermal insulation, a boon for regulating temperatures within tanks and piping systems. This insulation prowess aids in conserving energy and mitigating heat transfer, essential considerations across various applications.
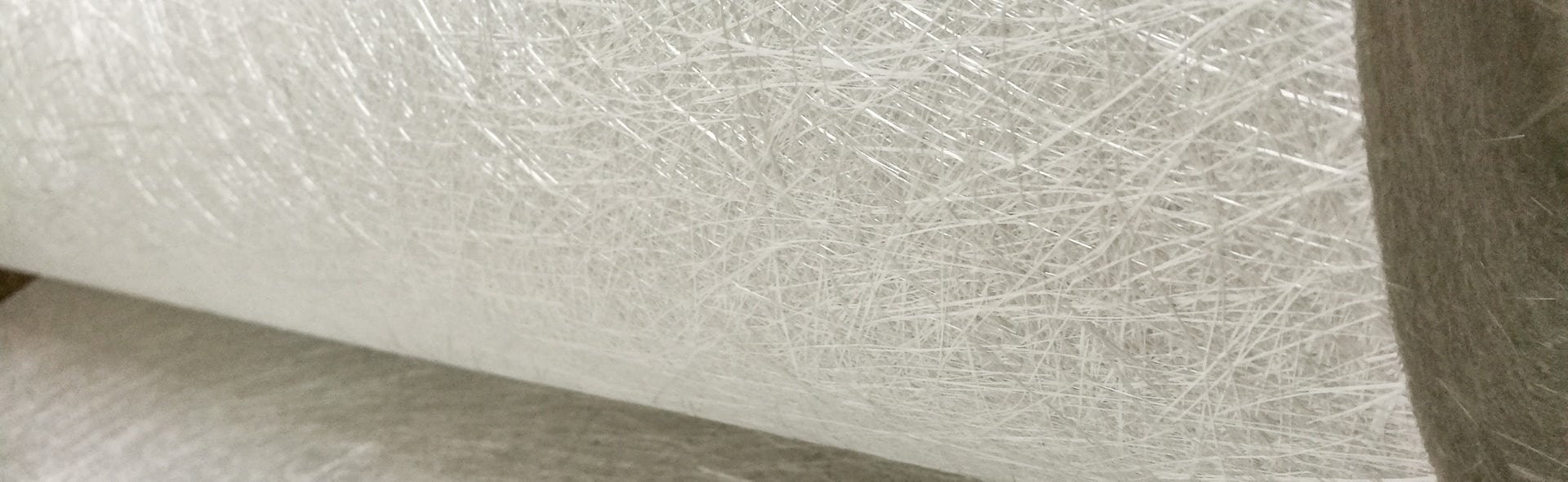
Applications of FRP in Tanks
Chemical Storage Tanks
FRP tanks are widely used in the chemical processing industry for storing corrosive chemicals and acids. Their corrosion resistance and high strength make them a reliable choice for maintaining the integrity of stored materials and ensuring the safety of the facility and personnel.
Water and Wastewater Treatment Tanks
In water treatment facilities, FRP tanks are employed for the storage of chemicals used in the treatment processes. Additionally, FRP is used in the construction of wastewater treatment tanks, where it can withstand the harsh and corrosive environments commonly found in sewage treatment facilities.
Oil and Gas Storage
FRP tanks are used for the storage of various petrochemical products, including crude oil, gasoline, and diesel fuel. Their corrosion resistance and ability to handle high-capacity storage make them a valuable asset in the oil and gas industry.
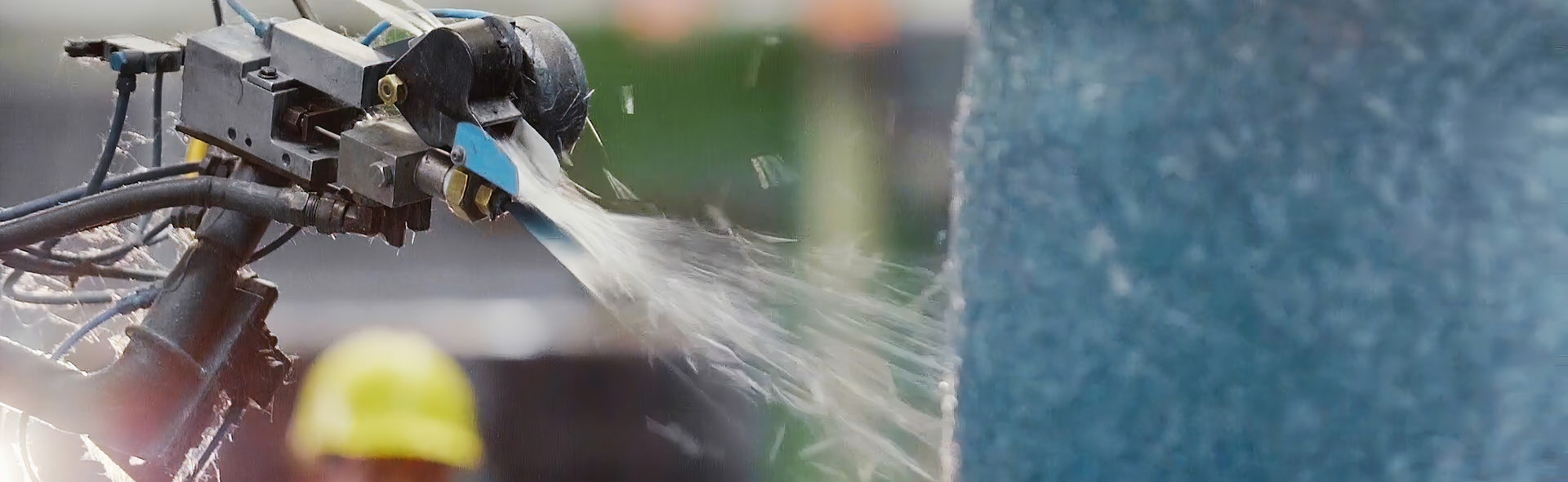
Applications of FRP in Absorbers
Air Pollution Control
In industries where air pollution control is a priority, FRP absorbers are utilized to remove pollutants from exhaust gases. FRP's resistance to corrosive gases and its ability to handle high temperatures make it a dependable choice for these applications.
Scrubbers
FRP scrubbers are commonly used to remove harmful gases, such as sulfur dioxide, from industrial emissions. The versatility of FRP allows for the design of efficient and customized scrubber systems that can effectively mitigate air pollution.
Applications of FRP in Piping
Chemical Transfer Lines
FRP piping systems are extensively used in the chemical industry for the safe and efficient transfer of corrosive chemicals. The material's corrosion resistance ensures that the integrity of the piping is maintained, and the risk of leaks or contamination is minimized.
Water and Sewage Piping
In municipal water and sewage systems, FRP pipes are used for their longevity and resistance to corrosion. These pipes can withstand the harsh conditions of underground burial and provide a cost-effective solution for water and sewage transport.
Applications of FRP in Flue Gas Ducts
Power Plants
Flue gas ducts in power plants are exposed to high temperatures and corrosive gases. FRP is employed in these ducts to handle the extreme conditions and ensure the safe removal of flue gases.
Industrial Exhaust Systems
In various industrial settings, exhaust systems are necessary to remove harmful fumes and gases. FRP flue gas ducts provide the necessary durability and corrosion resistance to meet the demands of these environments.
Conclusion
Fiberglass Reinforced Plastics (FRP) have earned their place as a versatile and reliable material in a wide range of applications. With their corrosion resistance, high strength-to-weight ratio, design flexibility, UV resistance, and thermal insulation properties, FRP composites are an ideal choice for use in tanks, absorbers, piping, and flue gas ducts. Whether it's safeguarding against corrosive substances in chemical processing or ensuring the safe transport of water and sewage in municipal systems, FRP plays a crucial role in various industries, contributing to the durability and efficiency of critical infrastructure. As technology continues to advance, FRP materials are likely to find even more applications, further underscoring their importance in modern engineering and manufacturing.
FRP Products
The majority of FRP products, such as storage tanks, duct systems, chimney liners, duct systems and specialty products are cylindrical in shape. Yet the benefit of working with FRP is the endless possibilities as regards thickness, capacity for combination with other materials, mix of materials, and is therefore lightweight, with smooth surfaces and possesses good insulation properties. FRP can also be used for non-cylindrical applications: read about one of these projects.
FRP products are ideal for on-site production and installation. Our international team of certified laminators handle installation jobs for customers all over the world.
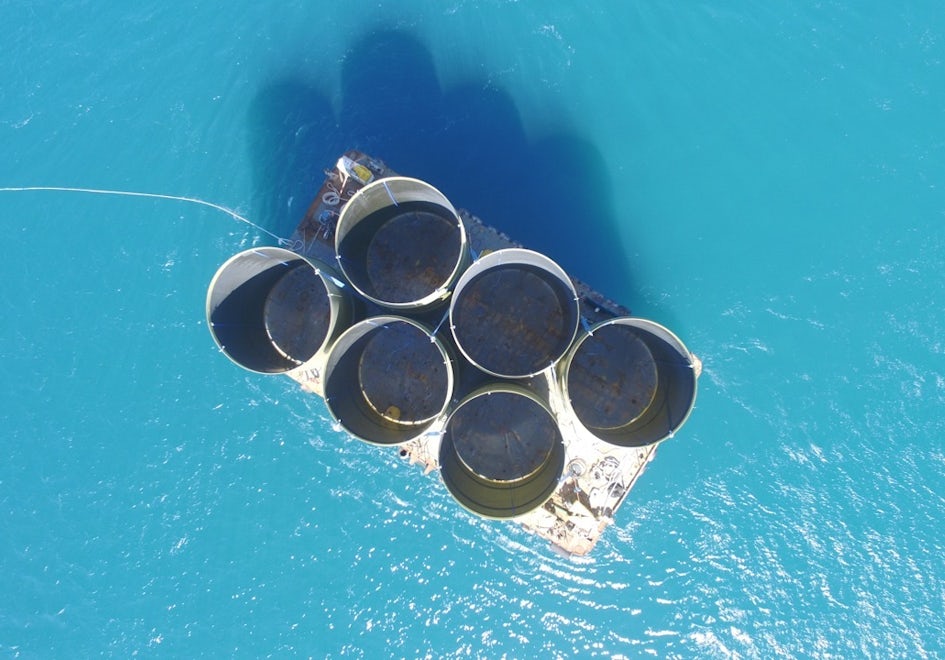