Power Plant Nikola Tesla TENT A
In the ever-evolving landscape of energy production, power plants are constantly striving to become more environmentally friendly and efficient. One notable example of this commitment is the Nikola Tesla TENT A Power Plant in Serbia, which has recently implemented a cutting-edge solution for flue gas desulfurization. This innovation includes a fiberglass reinforced duct and stack, designed and installed by Plasticon Projects.
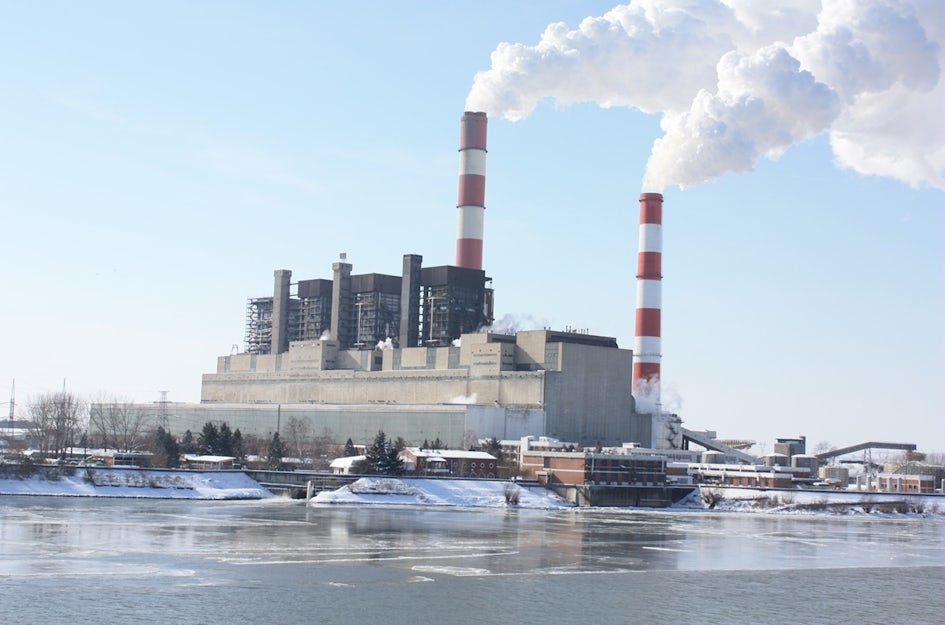

Desulfurization at TENT-A Nikola Tesla completed.
Plasticon Projects recently put the final touch on the revolutionary desulfurization facility at the Nikola Tesla A power plant. Their completion of two towering fiberglass reinforced plastic chimney stacks marks a significant milestone in environmental stewardship. These state-of-the-art structures exemplify the plant's commitment to reducing sulfur emissions, ensuring cleaner air for surrounding communities. Plasticon's expertise in crafting durable, high-performance materials has enabled the power plant to achieve its sustainability goals while maintaining operational efficiency.
Flue Gas Desulfurization: The Need for Cleaner Emissions
Flue gas desulfurization (FGD) is a critical component of modern power plant operations, particularly those that rely on fossil fuels such as coal and natural gas. The process of burning these fuels results in the release of sulfur dioxide (SO2) and other harmful pollutants into the atmosphere. These emissions have a detrimental impact on air quality, human health, and the environment, contributing to acid rain, smog, and respiratory problems.
In response to these challenges, environmental regulations have become increasingly stringent, necessitating the reduction of sulfur emissions. This is where FGD systems come into play, as they are designed to remove sulfur dioxide from the flue gas before it is released into the atmosphere. Various technologies are available for FGD, but the installation of a fiberglass reinforced duct and stack is an innovative approach that promises long-term durability and efficiency.
Plasticon Projects: Pioneering Corrosion-Resistant Solutions
Plasticon Projects, a globally recognized expert in the field of corrosion-resistant systems, has taken on the task of implementing a state-of-the-art FGD system at the Nikola Tesla Power Plant. The choice of Plasticon Projects is no coincidence, as their extensive experience in manufacturing and installing custom-made corrosion-resistant equipment made them the ideal candidate for this complex project.
Fiberglass Reinforced Duct and Stack: The Ideal Solution
The decision to utilize fiberglass reinforced duct and stack components at the Nikola Tesla Power Plant is a testament to the forward-thinking nature of the project. Fiberglass is renowned for its exceptional resistance to corrosion, making it a prime choice for applications in harsh, chemical-laden environments like FGD systems. Here's why this material is the perfect fit for the job:
- Corrosion Resistance: Fiberglass is highly resistant to corrosion, ensuring that the duct and stack will remain intact and functional for many years, even in the presence of corrosive flue gases.
- Durability: These components exhibit remarkable durability, even in extreme weather conditions, making them a cost-effective, long-term solution.
- Low Maintenance: Fiberglass reinforced systems require minimal maintenance, reducing operational costs and downtime.
- Lightweight: Fiberglass is lightweight, making it easier to transport and install, without compromising on strength and structural integrity.
Significance of the TENT A project
The implementation of the fiberglass reinforced duct and stack at the Nikola Tesla Power Plant signifies a commitment to sustainable energy production and environmental responsibility. By investing in advanced FGD technology, the plant not only ensures compliance with emission regulations but also contributes to the reduction of harmful pollutants, thereby enhancing the air quality and overall environmental well-being of the region.
Conclusion
The Nikola Tesla Power Plant's adoption of fiberglass reinforced duct and stack components, expertly manufactured and installed by Plasticon Projects, marks a significant step towards cleaner, more environmentally friendly energy production. This innovative approach to flue gas desulfurization not only showcases the power plant's dedication to reducing emissions but also serves as an exemplary model for other facilities seeking to improve their environmental footprint. With Plasticon Projects at the helm, the TENT A Power Plant reinforces its commitment to sustainability, ensuring a cleaner and healthier future for all.