Die Installation eines korrosionsbeständigen Glasfaser-Schornsteinliners in einem Betonschornstein im Kraftwerk Turów (Polen)
Fallstudie: FRP-Schornsteine und -Kanäle, einschließlich Bypass-System für das Kraftwerk Turów
Geschrieben von J.W. Warnar
Jahr der Veröffentlichung: 2016
Plasticon Composites International Contracting BV
Standort: Hengelo, Overijssel, Niederlande
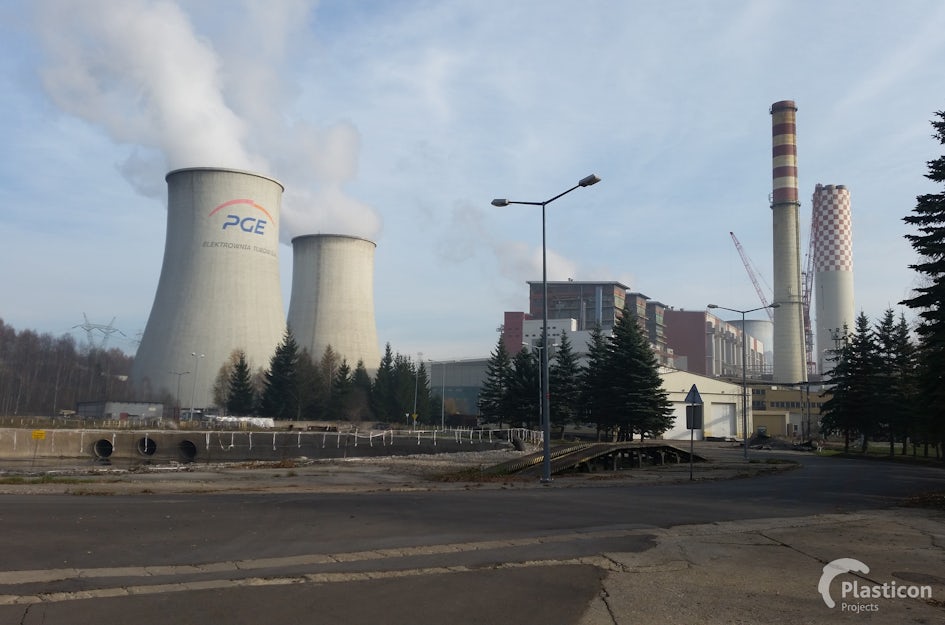
Zusammenfassung
Die PGE-Gruppe, Polska Grupa Energetyczna, ein führendes Energieunternehmen in Polen, investierte in umweltfreundliche Ausrüstungen und die Modernisierung ihrer bestehenden Kraftwerke. Teil dieser Investition war die Bestellung von drei neuen „Rauchgasentschwefelungs“-Anlagen, die auf der Sprühung einer Kalksteinsuspension in das Rauchgas basieren (nasse FGD). Die Anlagen wurden für die Blockeinheiten 4, 5 und 6 des Kraftwerks Turów in Bogatynia, Polen, entwickelt, das mit Braunkohle und Biomasse betrieben wird.
Jede Anlage ist für einen maximalen Rauchgasdurchfluss von 1.280.000 Nm³/h mit einer maximalen SO2-Konzentration von 2.500 mg/m³ und einer Entfernung von ≥ 97,5 % ausgelegt. Nach der Installation der drei Linien arbeitet die Rauchgasentschwefelungsanlage bei einer Temperatur von 70 °C und unter normalen Bedingungen. Während der Bauphase waren die Rauchgasentschwefelungsanlagen der Einheiten 4 und 6 jedoch nicht in Betrieb; während dieser Zeit arbeiteten die Einheiten unter Bypass-Bedingungen. Sobald die letzte Einheit (Nummer 5) installiert war, war das gesamte System für die Rauchgasentschwefelung betriebsbereit.
Während des Bypass-Betriebs (Einheit 4, 2 Jahre) konnte die Temperatur des Systems bis zu maximal 160 °C erreichen (für zwei Stunden, normal 141 °C) und unter einer maximalen SO2-Konzentration betrieben werden.
Die drei bestehenden Schornsteinliners, die aus Borosilikatblöcken bestanden, mussten ersetzt werden, da dieses Auskleidungsmaterial nicht die richtige Wahl für die Rauchgasentschwefelungsanlage dieses neuen Kraftwerks war. Die Ingenieure von PGE entschieden sich, glasfaserverstärkten Kunststoff (FRP) für den Bau der 700 Meter hohen Schornsteinliner und aller Kanalsysteme zu verwenden, aufgrund der feuchten Umstände und der großen Temperaturunterschiede (20 – 160 °C).
Die Herausforderung dieses Projekts für Plasticon Composites war der kurze Bauzeitraum, den die PGE-Gruppe vorgab. PGE bestand darauf, die Ziegel-Schornsteinverkleidung zu demolieren und den neuen Glasfaser-Schornsteinliner innerhalb eines Zeitrahmens von 40 Tagen zu installieren. Zu diesem Zeitpunkt hatte Plasticon Composites nur 25 Tage Zeit, um einen neuen Schornsteinliner mit einem Durchmesser von 5.300 mm und einer Höhe von 120 Metern zu installieren.
Dieses Papier beschreibt die Realisierung dieses anspruchsvollen Installationsauftrags, den Plasticon Composites ausführte, sowie die Möglichkeiten von Glasfaser und die Konstruktionsmethode eines Glasfaser-Schornsteinliners und -Kanals.

Location: Bogatynia, Poland
Rauchgasentschwefelung im Kraftwerk Turów (Polen)
Projektumfang
Das Kraftwerk Turów besteht aus sechs Blöcken mit jeweils 200 MW. Um die Umweltanforderungen zu erfüllen, entschied sich die PGE-Gruppe, in die Rauchgasentschwefelung (FGD) für drei der bestehenden Produktionslinien (Einheit 4-6) zu investieren. Die drei bestehenden Schornsteinliner mussten durch ein anderes Material ersetzt werden, da die vorhandenen Liner nicht beständig gegenüber den neuen FGD-Bedingungen waren und zudem bereits mehr als 10 Jahre in Betrieb waren.
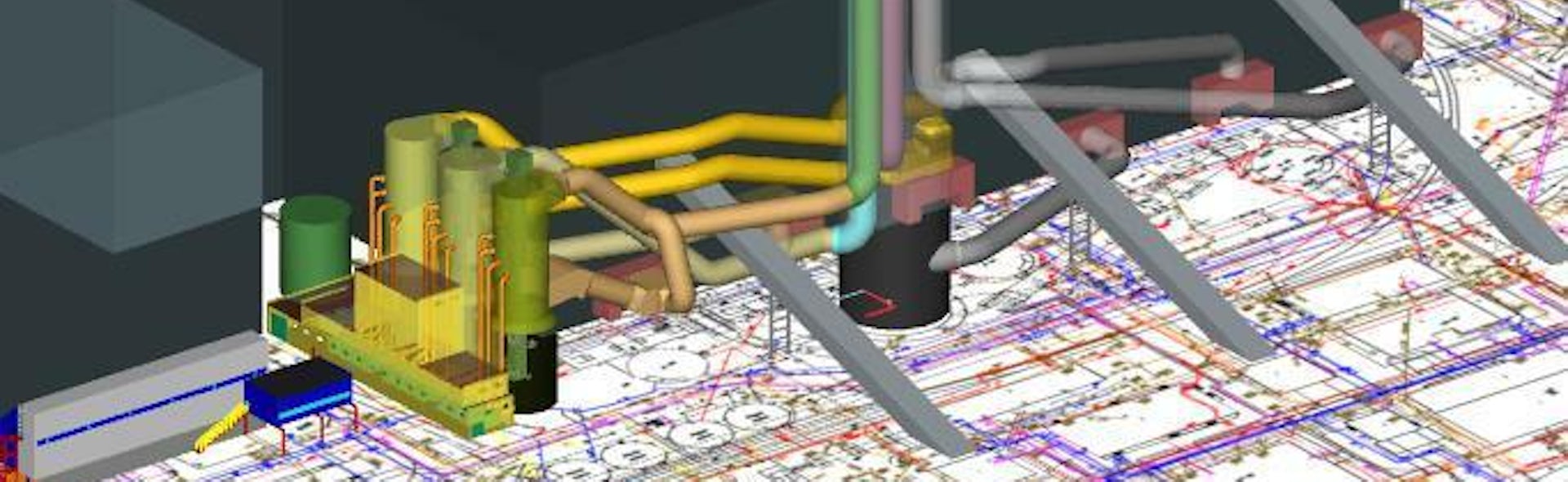
Abbildung 1: Der Aufbau des Kraftwerks mit FGD für die Einheiten 4-6.
Das FGD-System für die Einheiten 4–6 besteht aus einem Schornsteinliner von jeweils 120 Metern und etwa 330 Metern Kanalarbeiten. Der Durchmesser des gesamten Systems betrug 5.300 mm.
Designkriterien
Einführung
Im Jahr 2010 führte PGE eine Machbarkeitsstudie zur Auswahl des richtigen Materials für die Absorber, die Kanäle und den Schornsteinliner durch. Basierend auf den folgenden Kriterien entschieden sie sich für glasfaserverstärkten Polyester (FRP) als die richtige Wahl für die Rauchgasentschwefelungsanlage dieses neuen Kraftwerks. Die Kriterien:
- Chemische (und Korrosions-) Beständigkeit
- Temperaturbeständigkeit
- Aschenbelastung
- Lebensdauer und Garantiezeitraum
- Installationszeit des Schornsteinliners
- Kosten
Chemische Beständigkeit
Jede Einheit ist für einen maximalen Rauchgasdurchfluss von 1.280.000 Nm³/h ausgelegt, mit einer Zusammensetzung des Gases gemäß Tabelle 1.
Rauchgaszusammensetzung
Die Ingenieure von PGE entschieden, dass die drei bestehenden Schornsteinliner, die aus Borosilikatblöcken bestanden, aus zwei Gründen ersetzt werden mussten: Erstens aufgrund der feuchten Bedingungen des FGD-Systems. Zweitens aufgrund der Konzentration von Wasserstofffluorid (HF) im Gasstrom. Um diese Betriebsbedingungen zu erfüllen, wäre Glasfaser, legiertes oder titanbeschichtetes Stahl das richtige Konstruktionsmaterial.
Temperaturbeständigkeit
Normalerweise würde die Rauchgasentschwefelungsanlage bei einer Temperatur von 70 °C arbeiten. Während der Bauphase würde jedoch die Rauchgasentschwefelung der Einheiten 4 und 6 nicht operativ sein; diese Einheiten müssten unter Bypass-Bedingungen betrieben werden, wodurch höhere Temperaturen als normal erreicht werden würden. Sobald die letzte Einheit (5) installiert war, würde das gesamte System für die Rauchgasentschwefelung betriebsbereit sein.
Während des Bypass-Betriebs (Einheit 4 über zwei Jahre) könnte die Temperatur des Systems bis zu maximal 163 °C (für 2 Stunden, normal 141 °C) erreichen und unter maximaler SO2-Konzentration betrieben werden. Das Systemdesign basierte auf 22 Abschaltungen pro Jahr. Diese großen, wiederholten Temperaturschwankungen (20 – 160 °C, 22 Abschaltungen pro Jahr) waren sehr wichtig bei der Entscheidung für das richtige Konstruktionsmaterial. Glasfaser kann diese extremen Temperaturschwankungen perfekt aushalten.
Aschenbelastung
Die erwartete Aschenbelastung in den Kanälen (150 kg/m²), das Gewicht des Kanals selbst und die Isolierungseigenschaften des Materials waren wichtige Kriterien für das Design der Stahlträgerkonstruktion. FRP ist ein leichtes Material, besonders im Vergleich zu Stahl mit Borosilikatblöcken, was zu einer Einsparung von 25-30% an Stahlträgern im Design führte. Darüber hinaus ist Glasfaser auch besser resistent gegen die übermäßige Menge an Kondensat, das sich in den Kanalsektionen aufgrund der ausgezeichneten Isoliereigenschaften ansammelt.
Lebensdauer und Garantiezeitraum
PGE bestand auf einer langen Lebensdauer (> 30 Jahre) der Prozessausrüstung und forderte daher eine Garantiezeit von fünf Jahren, basierend auf den maximalen Designwerten. Glasfaser kann diese Lebensdauer problemlos erreichen, insbesondere unter den Bedingungen der Rauchgasentschwefelung. Die ersten Glasfaserliner für FGD wurden bereits 1973 in Salt Lake City, USA (Brady 2015), und vor 21 Jahren in Ingolstadt, Deutschland (van Buren 2014), installiert. Die ersten Schornsteine für Müllverbrennungsanlagen, bei denen die Betriebsbedingungen im Allgemeinen extremere sind, wurden 1985 in der Müllverbrennungsanlage Rotterdam (AVR) installiert.
Basierend auf der Erfahrung mit FRP war eine Garantiezeit von 60 Monaten oder fünf Jahren nach der Inbetriebnahme des Kraftwerks kein Problem. Diese Anforderung konnte problemlos von Plasticon Composites erfüllt werden.
Installationszeit des Schornsteinliners
PGE bestand darauf, den alten Borosilikat-Ziegel-Schornsteinliner abzubrechen und den neuen Schornsteinliner innerhalb eines Zeitrahmens von 40 Tagen zu installieren. Plasticon Composites hatte 25 Tage Zeit, einen neuen Schornsteinliner mit einem Durchmesser von 5.300 mm und einer Höhe von 120 Metern zu installieren, einschließlich des entsprechenden Bypass-Abschnitts, während die anderen fünf Blöcke des Kraftwerks in Betrieb blieben. Diese kurze Installationszeit sollte eine lange Stillstandszeit des Kraftwerks vermeiden, was hohe Kosten verursacht hätte.
Das Kraftwerk war voll ausgelastet, daher wäre der Verlust einer Linie über einen längeren Zeitraum sehr teuer und unzulässig gewesen. PGE hatte bereits die Investition in einen zusätzlichen Block von 200 MW eingeplant, um den Bedürfnissen ihres Kunden gerecht zu werden. Plasticon Composites legte einen sehr detaillierten Plan für die Installation des neuen Glasfaser-Schornsteinliners in maximal 25 Tagen vor. Die Installation des ersten Liners einschließlich Bypass dauerte 25 Arbeitstage. Die Installation des letzten Liners war innerhalb von 19 Arbeitstagen abgeschlossen.
Kosten
PGE führte auch einen Kostenvergleich verschiedener Materialien durch und kam zu dem gleichen Ergebnis, das bereits von Herrn Victor Bochicchio auf der ICCT-Konferenz in Prag 2014 vorgestellt wurde (siehe Tabelle 2).
Kosten der Auskleidungsmaterialien
Fazit
Basierend auf den oben genannten Designkriterien haben die Ingenieure von PGE eine Design-Spezifikation erstellt und empfehlen, Glasfaser-Material für die Konstruktion der Schornsteinliner, Kanalsysteme und Bypass-Systeme anzuwenden. FRP-Material hat sich als mechanisch robust erwiesen und bietet eine hervorragende chemische Beständigkeit. Darüber hinaus sind die Temperaturbeständigkeit und die lange Lebensdauer des Materials wichtige Kriterien, um das bevorzugte Material auszuwählen. Und nicht zuletzt trägt die wettbewerbsfähige Preisgestaltung für die Konstruktion eines FRP-Schornsteinliners und Kanalsystems zu der Feststellung bei, dass die Anwendung von FRP eine gut durchdachte Lösung ist.
Produktion des Schornsteinliners und der Kanäle
Filament-Wickeln der glasfaserverstärkten Polyester (FRP) Hüllen
Zunächst wurde der Schornsteinliner gemäß den extremsten Designbedingungen entworfen, indem eine statische Berechnung nach den CICIND-, EN- oder ASTM-Normen durchgeführt wurde. Diese statische Berechnung wurde durch die Durchführung einer Finite-Elemente-Analyse (FEA) überprüft, wobei die durch Druck, Temperatur, Asche, Gewichte usw. verursachten Belastungen berücksichtigt wurden.


Abbildung 2: Die FEA des Schornsteinliner-Moduls 4
Neben dieser statischen Berechnung wurde eine Strömungsanalyse und eine Kondensatberechnung durchgeführt.
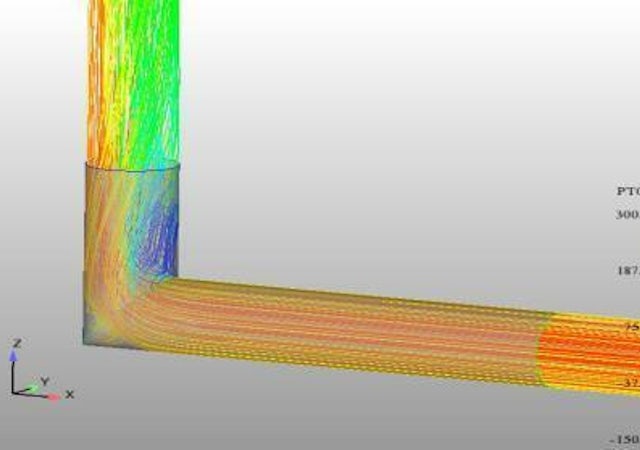
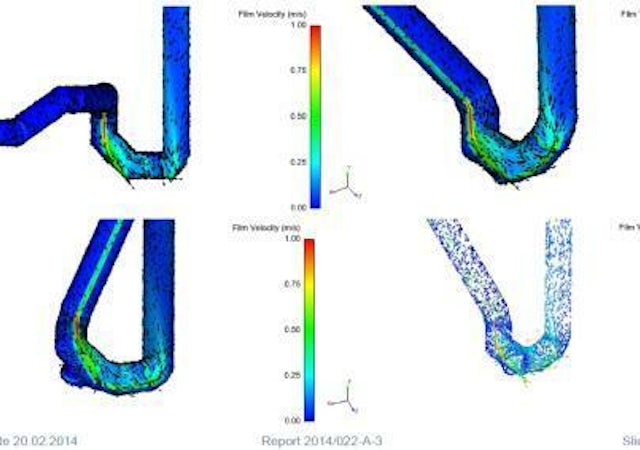
Abbildung 3: Die Strömungsanalyse eines Kanals in einem Kühlturm und eine Kondensatberechnung des Moduls 4 des Schornsteinliners von Turów.
Schornsteinliner und Kanäle mit großen Durchmessern werden vor Ort in einer temporären Einrichtung, der sogenannten „On Site Winding Machine“ (OSWM), produziert. Diese Einrichtung musste im Sommer (mit Temperaturen bis zu 45°C) und im Winter (mit Temperaturen bis zu -35°C) klimatisiert werden. Die OSWM wird aus ISO-Containern oder einem doppelwandigen Zelt gebaut. In dieser temporären Einrichtung werden Zylinder oder Hüllen mit einer Höhe von 6 Metern oder 10 Metern (je nach verwendeter Maschine) durch Filament-Wickeln hergestellt. Jede Hülle besteht aus einer chemischen Barrierschicht (2,5 mm) und Verstärkungsschichten auf der Basis von DERAKANETM 470 HT Epoxy Vinyl Ester Resin (einem Hochtemperaturharz) sowie Wickel- und Sprüh-Roving. Für die Kanäle wurden die Verstärkungsschichten mit unidirektionalen Kernmatten aufgebaut, um die Längssteifigkeit aufgrund der Biegung der Kanäle zwischen zwei Stützen zu gewährleisten. Für das Projekt in Turów produzierte Plasticon Composites in etwa 14 Monaten ca. 700 Meter Rohr oder 126 Zylinder.
Vor-Montage der Hüllen
Um die Bedingung zu erfüllen, den Schornsteinliner innerhalb von 25 Tagen zu installieren, bereitete Plasticon Composites Segmente von 24 Metern Länge vor, die aus vier Hüllen bestanden. Diese Segmente waren noch einfach zu handhaben (ca. 25 Tonnen) und konnten mit einem Kran gehoben werden.
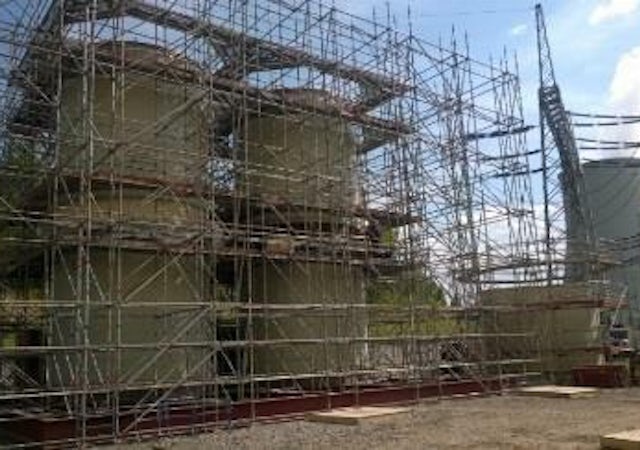
Abbildung 4: Vor-Montage der Hüllen.
Installation des Schornsteinliners und der Kanäle
Abriss des bestehenden Schornsteinliners
Ein Subunternehmer von PGE kümmerte sich um den Abriss des bestehenden Schornsteinliners. Sie entfernten jeden Borosilikatziegel über den unteren Ausgang des Beton-Schornsteins. Während dieses Abrisses war es nicht möglich, den neuen Schornsteinliner im Beton-Schornstein vorzubereiten, obwohl der Platz vorhanden war. Es war nicht sicher, und während des Abrisses wurde viel Staub erzeugt. Der Abriss des Ziegel-Liners dauerte 15 Tage.Installation des Schornsteinliners Einheit 4
Plasticon Composites erstellte einen detaillierten Installationsplan, um sicherzustellen, dass der maximale Installationszeitraum von 25 Tagen nicht überschritten wurde und um eine mögliche Strafe von 85.000 € pro Tag aufgrund einer verlängerten Stilllegung des Kraftwerks zu vermeiden. Es war klar, dass die Installation des neuen Schornsteinliners nicht im unteren Teil des Beton-Schornsteins durchgeführt werden konnte. Der Abriss des Ziegel-Liners verursachte viel Staub, und die HSE-Bedingungen konnten nicht gewährleistet werden. Das bedeutete, dass die Installation über den Einlass oder den Auslass des Beton-Schornsteins erfolgen musste. Da der Einlass während des Abrisses blockiert war und der Zeitrahmen (25 Tage) zu kurz war, um den neuen Glasfaser-Schornsteinliner und By-Pass aus den 25 Hüllen mit je 6 Metern zu bauen, war dies keine Option.

Abbildung 5: Installation der vor-montierten Hüllen.
Die Nutzung des Auslasses war also die einzige Option. Durch den Bau von Segmenten von 24 Metern konnte die Installation in 25 Tagen abgeschlossen werden. In diesem Zeitraum wurden die 24-Meter-Hüllen, das Flüssigkeitsauffangsystem, der Regenschutz, der Bogen, der By-Pass und alle Stahlstützen installiert, und die gesamte Laminierungsarbeit wurde in zwei Schichten durchgeführt.
Installation der Rohrleitungen
Die Installation der Rohrleitungen wurde separat durchgeführt. Alle Rohrleitungen sind mit einer 50 mm PU-Isolierung versehen, um Kondensation zu vermeiden. Obwohl Fiberglas im Vergleich zu Stahl ein Isolator ist, verlangte PGE, dass alle Teile außerhalb des Betonturms isoliert werden. Die Isolierung der Fiberglashüllen wurde direkt bei der Produktion der Hülle vorgenommen, sodass es sich um eine geschlossene Struktur mit hoher Isolierung handelt. Die Rohre wurden in Segmenten von 23 Metern Länge und 26 Tonnen installiert, um Störungen während der Installation aller anderen Komponenten im Kraftwerk zu vermeiden, indem die maximale Kapazität des großen Kranes genutzt wurde.


Abbildung 6: Transport und Installation der Rohrleitungen.
Entwicklungen im FRP-Geschäft
Variable Form
Jeder Kaminliner oder Rohrleitung aus Fiberglas hat aufgrund der Kapazität des Kraftwerks und des Prozessdesigns der Rauchgasentschwefelung seine eigenen Abmessungen. Um wettbewerbsfähig zu bleiben, entwarf Plasticon Composites eine variable Form, mit der jeder Durchmesser mit einer einzigen Form produziert werden kann. Diese Form besteht aus Fiberglaslamellen und kann von 7 bis 12,5 Metern Durchmesser oder 12 bis 20 Metern Durchmesser variiert werden.
FRP Absorber
Nun, da es möglich ist, große Durchmesser von Fiberglas-Kaminlinern, Rohrleitungen und Tanks vor Ort zu produzieren, sind auch Ingenieurbüros daran interessiert, große Durchmesser von Absorbern aus Fiberglas herzustellen, anstelle der konservativen Materialien wie Beton/PP oder Fliesenbeschichtungen oder Stahl/Gummi. Der Nachteil dieser Materialien ist ihre hohe Korrosion, lange Bauzeit und hohe Kosten. Die ersten Absorber wurden bereits in den achtziger Jahren in den USA und in den neunziger Jahren in Europa gebaut. Ein schönes Beispiel sind die beiden Absorber mit einem Durchmesser von 9 Metern und einer Höhe von 49 Metern im Kraftwerk PCK Schwedt. Es ist sogar möglich, Absorber mit einem Durchmesser von bis zu 30 Metern zu produzieren.


Figure 7: A fiberglass scrubber of 30-meter diameter.
Die Absorber der Bowen-Kraftwerksanlage, die 2007 gebaut wurde, haben einen Durchmesser von 30 Metern und eine Höhe von 20 Metern. Diese Absorber, insgesamt 4 Stück, wurden nach der Chiyoda-Lizenz entworfen.
Referenzen
Bochicchio V, 2014. Ein Überblick über Beschichtungsmaterialien für den Einsatz bei der Renovierung bestehender Kamine von Kraftwerken, ICCI 2014 Prag.
Brady B, 2015. Entwicklung von GRP in der Kaminindustrie, CICIND-Konferenz 2015 Boston.
Buren, van A, 2014. Kompositlösungen als Problemlöser in industriellen Kaminen und Kühltürmen, ICCT 2014 Prag.
Plasticon Projects ist bereit, Sie in jeder Hinsicht zu unterstützen.
Gemeinsam können wir die Spitze erreichen.
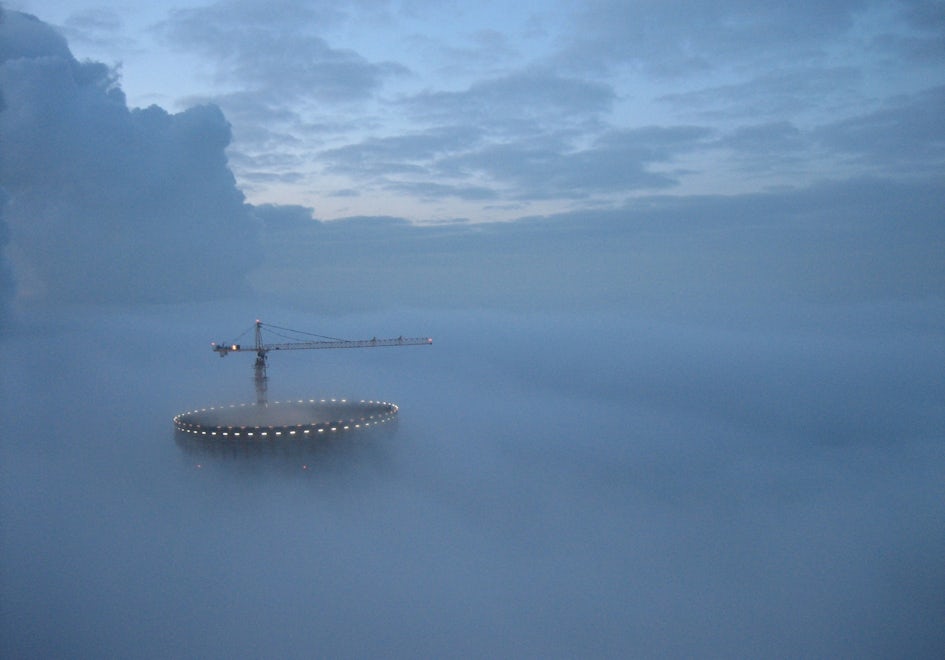