Project
Full FRP Chimney liner, FGD process, transportation of gasses
- CustomerElectricity Company
- LocationAsia / Middle East
- Project executed2012
- DimensionsDiameter: 7,000 mm High of Stack: 200 meter
- MediumFlue gas, H2S
- TemperatureDesign Temperature: + 80° C
-
Market segmentPower & Energy
The client, an Electric Company in Asia/Middle East, selected Plasticon Composites International Contracting as an experienced partner for the design, fabrication with the On Site Winding Machine, supply and installation of this project.
The chimney was constructed on the Power Station Site. The power station is located along the Mediterranean seashore. The plant includes two existing coal-fired power stations. The flue gas desulfurization (FGD) absorber was based on wet limestone technology producing commercial quality gypsum as by product. From the absorber the flue gas is carried to one new 250 m concrete chimney equipped with two FRP liners, one liner for each generating unit. The existing 300 m concrete chimney equipped with one common liner for both units, act as the hot by-pass stack for some years and was dismantled later.
The liner is a 200m Ø 7m cylinder, beginning at elevation 80 m at the liner expansion joint upper flange and ending at elevation 250 m, it is supported 50m under the top of the chimney, at elevation 200 m, and deflected with the concrete chimney. The supply of recirculation piping systems was included in the scope of the project as well.
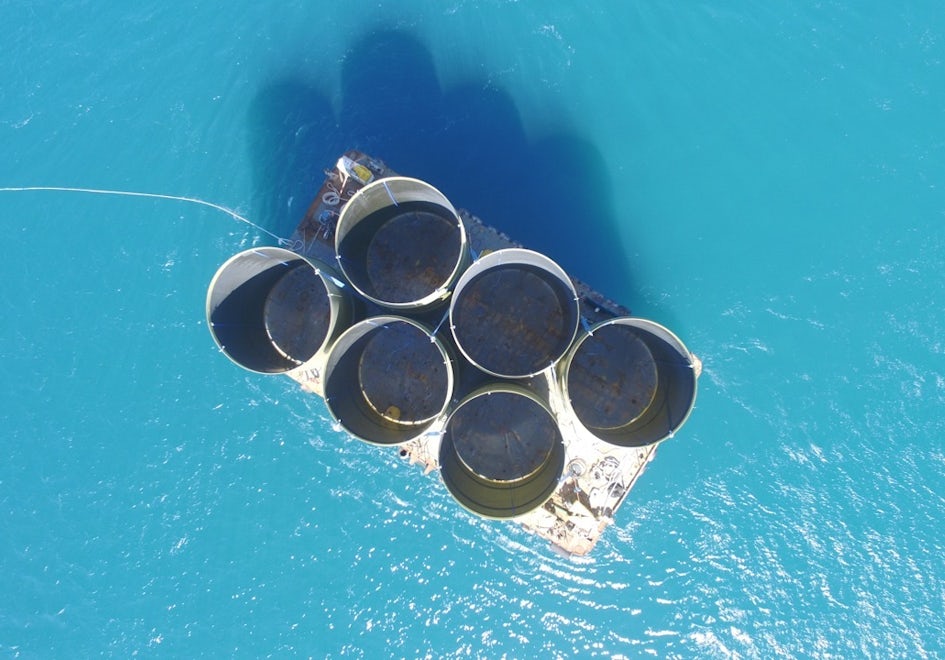